Technology Project
SupErLaTiv
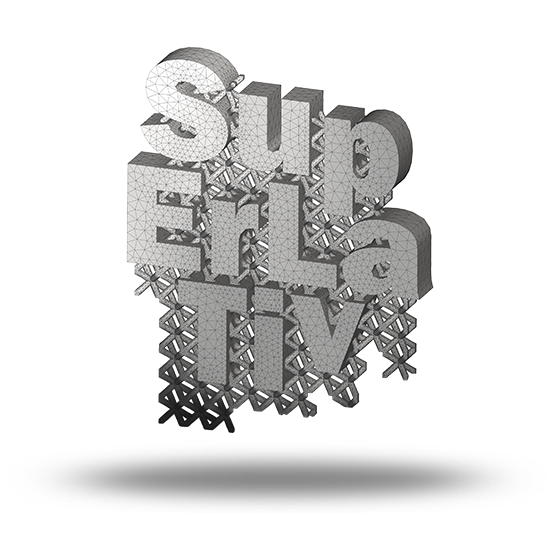
Objective:
Simulation protected automatic support structure creation for laser based additive manufacturing
Partners:
Duration: 01.04.2019 - 31.03.2021
Introduction: Support structures
Supporting structures are auxiliary geometries for the manufacturing process and not part of the actual component. In Laser Beam Melting (LBM), such structures serve several purposes. On the one hand, they enable the production of component overhang areas, typically in the range of 45° to 90° of the surface normal to the X-Y surface/building platform, based on experience. On the other hand, they serve as a connecting element between component and building platform and thereby take over three essential functions:
1) They enable an extended dissipation of the heat of fusion introduced by the laser energy from the molten pool or the solidifying weld bead.
2) The support structures absorb the mechanical forces acting on the component and mainly caused by thermally induced residual stresses and fix the component in its position on the building platform or in the installation space.
3) Furthermore, support structures are used to separate the component and the building panel from each other without damage.
Today, support structures are generated as far as possible automatically from simple control geometries, such as thin walls, cylinders or truncated cones within the CAM software. The CAM software contains algorithms that create the support structure on the component in a regular division depending on the component orientation and predefined overhang limit angle. The determination of where support structures are presumably necessary is based on purely geometric criteria, which can lead to unnecessary support as well as to missing support in critical areas. In the post-processing process, the support structure is then removed from the component by hand using current state-of-the-art technology. Figure 1 illustrates the tension between the target values of component quality and economic efficiency in the design of support structures in LBM.
Figure 1: Design of support structure in the area of conflict between component quality and economy
Users of the additive manufacturing technology laser beam melting therefore need to find new optimization approaches for the design of support structures in the area of conflict between component quality and economic efficiency. The premise here is: "As much support structure as necessary, but as little as possible". Current approaches in this regard are aimed primarily at reducing the relative density of the support structures by using, for example, grid structures. The mechanical properties of the support are mainly considered, and to some extent also the thermal properties.
Within the data and construction process preparation, many time-consuming manual steps are often necessary for the preparation of the support. For the manufacturing process, each additional volume element to be built, i.e. each additional support structure, means an increase in manufacturing costs and time. Often, component errors and process interruptions also occur due to incorrectly designed support structures, which may result in data adjustments and a new production. In component reworking, i.e. at the end of the process chain, the separation of support structures and the reworking of connection surfaces on the component are necessary.
Project goals
The aim of the project is to extend this previously geometry-based creation and experience-driven optimization of support structures by a simulative approach or to replace it with this approach. This should allow for a more targeted placement and, if possible, geometric design of supports in order to keep the manual and mechanical effort for creating and removing the support as low as possible while ensuring excellent component quality and an error-free construction process. For this purpose, the three concrete sub-goals shown in figure 2 are addressed within this project.
Figure 2: Objectives of the SupErLaTiv project
The objectives of this project address the current aspects of the AGENT-3D-Roadmap 3.0 "Accelerated product development for prototypes", "Changing the product creation process" in a narrow sense and "Energy efficiency, waste management" in a broader sense. The current state of the art is extended by new simulation-based approaches and analyses of the influence of selected process parameters (here: laser and exposure parameters) for the production of support structures. This is an important contribution to the extension of the process understanding and the economical as well as quality-conscious production of components by means of LBM.
Implementation
In order to achieve the above objectives, the existing simulation method is to be extended. Simufact Additive is a software product with which the build-up process of the LBM can be simulated and the resulting residual stresses and resulting distortion can be predicted (see Figure 3).
Figure 3: Representation of the component distortion simulated with Simufact Additive at different support placement using the AGENT-3D logo as an example
At present, this program offers two different calculation options: Firstly, it uses a purely mechanical calculation based on so-called inherent strains, in which the effects of transient heat input by the laser source are simulated by applying small, previously calibrated strains. On the other hand, thermal or thermo-mechanical coupled calculation allows a simplified transient simulation of the build-up process with consideration of this heat input. In the case of the purely mechanical calculation, thermal processes are not taken into account in favour of an extremely short calculation time. The user has to adapt his own process for each exposure strategy and each machine by means of calibration geometries.
With the availability of a simplified method for a transient thermo-mechanically coupled simulation, this calibration process can now be dispensed with. It forms the basis for the automatic optimization of the support structure planned in this project, which in addition to the mechanical aspects can also take heat dissipation into account. The main focus of the planned extension of the simulation methodology is the integration of the simulation of the construction process into an iterative procedure, in which on the one hand an insufficient support is identified and compensated by changes in the support structure, and on the other hand only slightly or not at all stressed parts of the support structure are removed or reduced in favour of a reduction of the support volume and a shortening of the construction time.
The results of the manufacturing simulation shall be used to derive criteria where supports with given thermo-mechanical properties are needed. The goal of the iteration process is to define defined criteria, such as the limitation of maximum distortion with minimum support.
For more efficiency in material-, machine- and process-related calibration, a generally valid procedure is to be developed, which includes methods of statistical design of experiments on the one hand and algorithms for the automated evaluation of calibration experiments until the required model parameters are determined on the other hand.
Figure 4: Project relevant competences of the project partners