Technology Project
FLOW 4.0
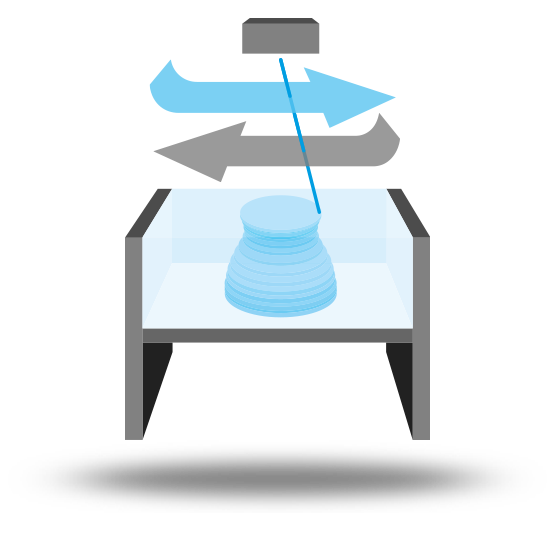
Objective:
Increasing the safety and efficiency of additive manufacturing processes through intelligent extraction technology
Partners:
Duration: 01.08.2019 - 31.07.2021
Increasing the safety and efficiency of additive manufacturing processes through intelligent extraction technology
The feasibility study Flow 4.0 focuses on the filter technology and analysis of the process gas during laser beam melting. The influence on process stability, component quality and air quality outside the system are evaluated. Relevant quality criteria for the manufactured component as well as the influencing variables from the system technology, the process and the used extraction and filter technology are evaluated. From this, control variables for product quality and measures for process and quality stabilisation are derived. This is done both for the qualification of data-based methods for process development, which are indispensable due to the complexity of the process and the process documentation required from a quality management point of view, and for economical and quality-compliant series production.
work plan of the project and the tasks of those involved in the project
Goals
The planned technology project Flow 4.0 addresses a fundamental key factor for the successful industrial application of additive manufacturing processes, in which the process stability influenced by the filter unit and the extraction process is significantly improved. The influence of the extraction and filtering technology used on component quality will be systematically evaluated. The economic efficiency is correlated with the product quality.
The main goals of the AGENT-3D consortium, which are to achieve industrial application maturity of additive manufacturing processes and their successful market implementation, are directly supported by Flow 4.0 by addressing the fields of action "environment", "simulation", "automation" and "economic efficiency"..
Influence of extraction and filter technology on the process
The needs-based adjustment of the extraction capacity of the installed filter technology, depending on the process gas used, contributes to the reduction of energy and flushing gas requirements as well as to the extension of maintenance intervals through a longer service life of the filters. Both features are not extensively optimised by the plant manufacturers.
The aim of the planned development is the process-integrated filter monitoring, predictive maintenance, automated, reproducible adjustment of the flow conditions with integrated measuring and control system. This also includes the complete integration of the separation unit into the overall plant concept.
Holistic, data-driven process optimization
Within the scope of Flow 4.0, methods of Technology Data Management (TDM) are applied to determine the model parameters for the material description, the load cases/process sequences and for calibration. For this purpose, technological data from the laser beam melting process and the separator unit as well as data from material and component testing are integrated on an operational level. The data stock thus obtained enables process optimization with novel methods of data analysis, such as machine learning.